Machine periphery
With its machine periphery, MINDA offers the direct interface upstream and downstream your converting machines and thus provides the complete solution within your plant. With the ADVECTOR and its different models, fully automatic smooth feeding of all applications from Mini- to Midline is possible. The customer-specific equipment of the Prefeeder by lateral or straight stack feeding, package turning, and variation of the transfer table as well as its possible movability ensures a solution for almost every application besides the standard one.
Due to the limited space available at our customers and the trend towards longer converting machines, we have optimized our ADVECTOR once again and responded to individual requirements with the ADVECTORbrevis.
Our FRACTOR quickly and gently separates your finished products from flat-bed and rotary die cutters. In this respect, one of our strengths is the individual adjustment to the respective converting machine. This allows die-cut sheets up to a working width of 3200 mm to be cut, which is no problem even with L nesting.
The product range is completed both by manual palletizing in stacking corners with the help of our semi-automatic palletizing machine and completely automated by robots or our simple palletizer STRATOR as well as STRATOR Duo as double palletizer.
Bundle conveyors are used for the discharge of the bundles. With the help of the Spherical Table and the Spherical Cross we turn the packages and transport them by 90°. In this way we create a wide variety of pallet patterns so that the goods arrive at their destination in the desired orientation.
Application of different Prefeeders
Product name | Application |
---|---|
ADVECTOR | for Midline applications and die cutters |
ADVECTORVerto | for Midline applications and die cutters |
ADVECTORBrevis | in front of flat-bed die cutting in combination with or without printing units |
Prefeeder ADVECTOR
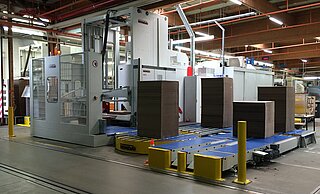
The ADVECTOR ensures optimized sheet feeding to printing lines, inliners, flat-bed and rotary die cutters and digital printing machines by creating a continuous shingling sheet flow.
With its extremely short installation length, due to the possibility of a lateral infeed, the ADVECTOR can be used almost everywhere - even under very constricted space conditions. This can also be realized with ADVECTORS that can be driven up. This creates more storage space and enables the machine operator to carry out a final quality check before the block is processed in the ADVECTOR.
Unlike conventional solutions, the stacks are not raised but directly processed in small packages. This enables the operator to mark, for example, a damaged area in the stack in the touch panel, which should not be processed. The ADVECTOR removes the stack up to the marking and the operator can then take out the damaged sheets. Furthermore, this concept ensures highest throughput rates, as the stack change time is reduced compared to conventional applications. Residual sheet discharge and infeed of the new stack take place in parallel. The internal buffer on the lifting table and in front of the shingling gate bridge the time of the stack change.
A hold-down device ensures that the separation process is trouble-free even with curved sheets. Thus, no sheets are pulled along unintentionally and subsequently the production process is not disturbed.
Advantages
- Easy handling for operators thanks to modern HMI touch panel
- No lifting of unnecessary weights by pick-up from stacks in packages
- Short installation length possible by lateral infeed
- Continuous shingling sheet flow even during stack change without any downtime
- Short machine set-up time by storing the order data
- Clean production and feeding area by complete elimination of hydraulics
Special features
- Telescopic transfer table adjustable to converting machine
- Optional construction and control of alignment pushers at the converting machine
- Gentle transport by continuous rubber-covered plastic chain
- Easy integration into existing structures
- Good access for sheet removal
- Free selection of operator side
- Exclusive use of electrical and pneumatic components
The further development of the MINDA Prefeeder ADVECTOR: The ADVECTORbrevis.
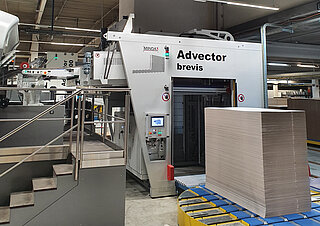
In contrast to the conventional ADVECTOR, the lifting process is carried out by the infeed conveyor and the packages are pushed directly in front of the shingling gate. Thus, we could save another 1.5 m in length. Combined with the lateral infeed, the material buffer may be realized near the ADVECTORbrevis.
The machine operators can carry out a final quality check - through perfect intervisibility - before the sheets are processed.
Other advantages of the ADVECTOR series have also been integrated in the ADVECTORbrevis, such as endless shingling sheet flow, continuous rubber-covered chain, exclusively pneumatic or electric drives, HMI touch panel, etc.
In addition, there is a free choice of residual sheet discharge, either in the direction of machine passage or laterally.
The ADVECTORbrevis is available for all flat-bed die-cutter combinations, with or without printing units. The sophisticated design also enables us to supply our customers with the ADVECTORbrevis as a complete assembly group, eliminating time-consuming efforts for on-site installations.
Advantages
- Short installation length by lateral infeed and discharge directly in front of the shingling gate
- Continuous shingling sheet flow even during stack changes without downtimes
- Easy handling for operators thanks to modern HMI touch panel
- Short machine set-up time by storing the order data
- Clean production and feeding area by complete elimination of hydraulics
- No assembly work on site, as delivery as a complete assembly group
Special features
- Telescopic transfer table adjustable to converting machine
- Residual sheet discharge in throughfeed direction or laterally
- Gentle transport by continuous rubber-covered plastic chain
- Easy integration into existing structures
- Good access for sheet removal
- Free selection of control side
- Exclusive use of electrical and pneumatic components
Prefeeder ADVECTORverto
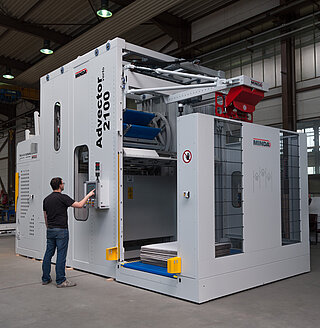
Based on the basic concept of the ADVECTOR, the ADVECTORverto is equipped with a turner. This can supply top printers and applications for an internal/double-sided print. The Verto offers even higher throughput rates due to the additional material buffer in the turner. Of course, it is also possible to use the infeed laterally here.
Advantages
- Easy handling for operators
- No lifting of unnecessary weights by pick-up from stacks in packages
- Short installation length possible by lateral infeed
- Continuous shingling sheet flow even during stack change without any downtime
- Short machine set-up time by storing the order data
- Clean production and feeding area
Special features
- Telescopic transfer table adjustable to converting machine
- Gentle transport by continuous rubber-covered plastic chain
- Easy integration into existing structures
- Good access for sheet removal
- Free selection of operator side
- Exclusive use of electrical and pneumatic components
Advector - Worldwide References
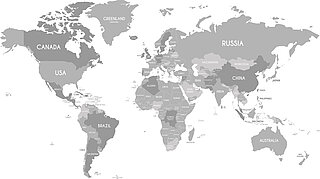
Denmark 2 Prefeeders in front of:
- 1 inliner machine with a working width of 3200 mm
- 1 flatbed die-cutter with a working width of 1600 mm
Norway 2 Prefeeders in front of:
- 1 inliner with a working width of 3200 mm
- 1 rotary die-cutter machine with a working width of 2800 mm
Sweden 1 Prefeeder in front of:
- 1 Prefeeder in front of an inline machine with a working width of 2400 mm
France 3 Prefeeders in front of:
- 2 inliners with a working width of 1700 - 2100 mm
- 1 flatbed die-cutter with a working width of 2100 mm
Belgium 1 Prefeeder in front of:
- 1 Prefeeder in front of an inline machine with a working width of 3200 mm
Netherlands 2 Prefeeders in front of:
- rotary die-cutters, each with a working width of 2800 mm
Austria 6 Prefeeders in front of:
- 1 inliner with a working width of 2400 mm
- 4 printing machines + die-cutters with a working width of 1700 - 2100 mm
- 1 flatbed die-cutter with a working width of 2100 mm
Switzerland 1 Prefeeder in front of:
- 1 Prefeeder in front of a flatbed die-cutter with a working width of 2100 mm
Poland 7 Prefeeders in front of:
- 3 Inliners, each with a working width of 3200 mm
- 2 flatbed die-cutters, each with a working width of 2100 mm
- 2 rotary die-cutters with a working width of 2800 - 3200 mm
Hungary 1 Prefeeder in front of:
- 1 Prefeeder in front of a printing machine + a die-cutter with a working width of 2100 mm
Czech Republic 2 Prefeeders in front of:
- 2 Prefeeders in front of inline machines, each with a working width of 2400 mm
- 1 Prefeeder in front of a rotary die-cutter with a working width of 3200 mm
- 1 Prefeeder in front of an inline machine with a working width of 2600 mm
- 1 Prefeeder in front of a flatbed die-cutter with a working width of 1700 mm
- 3 Prefeeders in front of inline machines with a working width of 2400 - 3200 mm
Germany 30 Prefeeders in front of:
- 11 inliners with a working width of 1880 - 3200 mm, 2 x execution as ADVECTORverto
- 9 flatbed die-cutters with a working width of 1700 - 2100 mm
- 7 printing machines + die-cutters with a working width of 2100 mm, 3 x execution as ADVECTORverto
- 1 digital printing machine with a working width of 2100 mm
- 2 rotary die-cutters with a working width of 2400 - 2800 mm
Denmark 2 Prefeeders in front of:
- 1 inliner machine with a working width of 3200 mm
- 1 flatbed die-cutter with a working width of 1600 mm
Norway 2 Prefeeders in front of:
- 1 inliner with a working width of 3200 mm
- 1 rotary die-cutter machine with a working width of 2800 mm
Sweden 1 Prefeeder in front of:
- 1 Prefeeder in front of an inline machine with a working width of 2400 mm
France 3 Prefeeders in front of:
- 2 inliners with a working width of 1700 - 2100 mm
- 1 flatbed die-cutter with a working width of 2100 mm
Belgium 1 Prefeeder in front of:
- 1 Prefeeder in front of an inline machine with a working width of 3200 mm
Netherlands 2 Prefeeders in front of:
- rotary die-cutters, each with a working width of 2800 mm
Austria 6 Prefeeders in front of:
- 1 inliner with a working width of 2400 mm
- 4 printing machines + die-cutters with a working width of 1700 - 2100 mm
- 1 flatbed die-cutter with a working width of 2100 mm
Switzerland 1 Prefeeder in front of:
- 1 Prefeeder in front of a flatbed die-cutter with a working width of 2100 mm
Poland 7 Prefeeders in front of:
- 3 Inliners, each with a working width of 3200 mm
- 2 flatbed die-cutters, each with a working width of 2100 mm
- 2 rotary die-cutters with a working width of 2800 - 3200 mm
Hungary 1 Prefeeder in front of:
- 1 Prefeeder in front of a printing machine + a die-cutter with a working width of 2100 mm
Czech Republic 2 Prefeeders in front of:
- 2 Prefeeders in front of inline machines, each with a working width of 2400 mm
- 1 Prefeeder in front of a rotary die-cutter with a working width of 3200 mm
- 1 Prefeeder in front of an inline machine with a working width of 2600 mm
- 1 Prefeeder in front of a flatbed die-cutter with a working width of 1700 mm
- 3 Prefeeders in front of inline machines with a working width of 2400 - 3200 mm
Germany 30 Prefeeders in front of:
- 11 inliners with a working width of 1880 - 3200 mm, 2 x execution as ADVECTORverto
- 9 flatbed die-cutters with a working width of 1700 - 2100 mm
- 7 printing machines + die-cutters with a working width of 2100 mm, 3 x execution as ADVECTORverto
- 1 digital printing machine with a working width of 2100 mm
- 2 rotary die-cutters with a working width of 2400 - 2800 mm
Breaker line/ Breaker - FRACTOR
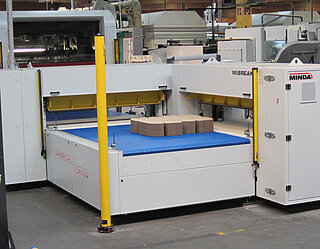
For the completion of palletizing lines in the area of flat-bed and rotary die cutters, the Fractor has been developed for different working widths up to 3,200 mm. The Fractor is used to separate die-cut sheets, when several finished products are produced from one die-cut sheet and must then be separated after the die-cutting process. The electronically working Fractor with adjustable and segmented bar features a high positioning accuracy and a simple operation. It is also suitable for L-form nesting. Due to the rubber-covered plastic chain only a low pressure is required so that the flutes of the sheets are not compressed during the separation process.
Breaker line
In the breaker line two breakers are arranged as line or angular version in order to separate the goods in length- as well as crosswise direction.
This installation allows dividing the separation process and thus leads to a higher throughput per hour. With the modular design and the variable installation possibilities the Fractor line provides applications for nearly all requirements.
Advantages
- Electrical drive, no hydraulics
- High positioning accuracy
- Easy handling for operators thanks to modern HMI touch panel
- Short installation length
- Adjustable, segmented bar
- Easy access to all components due to the movability of the FRACTOR
- High productivity by short cycle times
- Model with rubber-covered plastic chains
Special features
- High speed
- Electrical pressure device
- No pressure marks due to special chain
- No compression of the corrugated board by low pressure
- Very high safety standard
Corner turntables - Spherical Cross
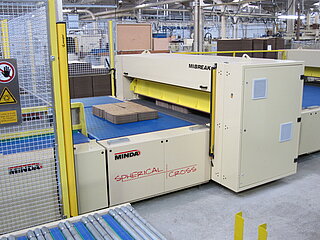
Corner turntables are used in transport lines when the direction is changed by 90° and products are to be fed in and out laterally.
A plastic chain with balls allows an easy and elegant execution of this task. Under the ball chain a light transport belt is arranged crosswise to the operating direction. For the lateral transport this belt is driven, the bundles or trays are moved against the operating direction of the belt and can be taken by the adjacent conveyor.
Advantages
- Minimal ball grid for smallest products
- No lifting required, thus no shearing and pinching zones
- Safe and gentle transport of adjacent products
- Transport in all four directions without restrictions
Special features
- Flat ball chain on transport belt
- No housing or safety fences necessary
- Installation size according to the products
Applications
Spherical Cross behind bundling machines
Up to now, right angle stations fed out the packages behind bundling machines. On the spherical cross the packages are transported at high speed on the ball chain and then laterally fed out to the right or left hand side by means of the transport belt. A superposed movement and fast cycle times can be realized.
Spherical Cross as sorting station
The Spherical Cross in extended design is used to sort goods to several in- and outlets. The goods are distributed in different directions without any switch points or mechanical impact. The contact-free change of direction allows a gentle shift in direction.
Turntable- Spherical Table
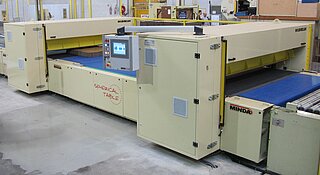
On the spherical table bundles and trays can be turned with free access by 90° or 180°. The turntable is equipped with a plastic chain with integrated balls. The product is centered above the turntable. The safe and exact rotation of the goods is ensured by turning the table while the chain remains unmoved. Then the goods are transported by means of the chain. As this process does not require any lifting movement, it does not lead to any dangerous pinch and shear zones. Thus, housing or safety fences are not necessary. The cycle time is shortened compared to conventional technology.
Advantages
- Minimum ball grid for smallest products of 200 mm x 200 mm
- No lifting required, thus no shearing and pinching zones
- Safe turning of adjacent products
- Any angle of rotation is possible
Applications
Spherical Table between breakers
The spherical table is positioned between two breakers as turning device in order to turn the bundles from the one breaker by 90° prior to feeding them to the second breaker.
Spherical Table in front of palletizing robot
The spherical table is positioned in front of a robot for load forming and turns the packages by 90° or 180°, if required.
Special features
- Flat ball chain on turntable
- No housing or safety fences necessary
- Installation size according to the product
Bundle conveyor
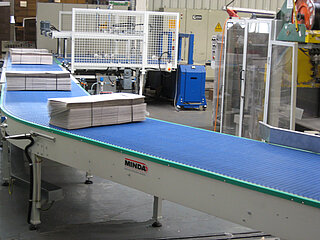
This curved plastic chain conveyor has been designed for the discharge of bundles behind folder gluers. Different curve radii even allow the application under limited space conditions for a safe and gentle transport.
Advantages
- Working width individually adjustable
- Different curves from 90° to 180° are available
- Gentle transport of unit loads
- Ideally suited for areas with high hygienic requirements
Semi-automatic palletizer
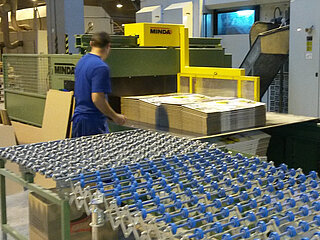
The semi-automatic palletizing is used to create stacks behind a converting machine and always works at the same ergonomic height.
The operator pushes the bundles onto the stacking plate, where packing patterns are built. After the complete layer has been created, the layer change is activated by means of a push-button.
Then the stacking plate moves back and the finished layer is positioned on the pallet.
RoboMate
In the corrugated industry, there are still many semi-automatic palletizers in the field being operated by a person. These components are often in a good condition and reach sufficient capacity for the requested application. Together with Maschinenbau u Konstruktion GmbH Elmshorn MINDA offers a robot for retrofitting which assumes the tasks of this operator. The robot - RoboMate - then performs the function of the operator and can carry out the work with a higher and more continuous performance. This increases the performance of the entire system in a minimum of space.
Advantages
This retrofitting provides the following advantages:
- High performance continuity
- More space-saving than a complete robot cell
- Optimum stacking pattern by creating individual layers
- Automatic creation of different packing patterns
- Manual mode provided at any time
Possible design
- Preparation of empty pallets with automatic positioning of the bottom sheets
- Feeding of intermediate sheets
- Turning of stacks, as required
Installation
An articulated arm robot, which performs the layer formation and also positions the required intermediate sheets, is laterally fixed at the customer’s semi-automatic machine. Depending on the packages being fed in bundles or non-bundled via a driven or a non-driven bundle transport, an alignment device with front stop and a discharge conveyor are to be added. The robot can pick up bundles up to 1,000 mm x 1,000 mm and form corresponding layers.
Palletizing robot
Robot for palletizing
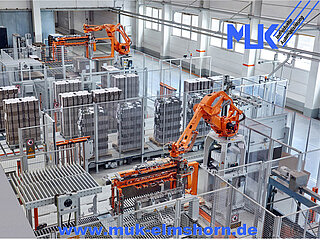
The palletizing robot is used for fully-automatic creation of stacks behind inliners, flat-bed die-cutters and rotational die-cutters.
The packs are automatically fed to the robot and can be turned, turned over or doubled up depending on the default stack formation pattern. The robot gripping system allows to pick-up one or several bundles at the same time and properly deposits them. Thanks to this flexibility there is no fixed reference required and any palletizing pattern can be created.
Automatic dispensing of the bottom protection sheets and intermediate layers is achieved by a linear unit equipped with injection suction cups.
Our partner for robot palletizing is Maschinenbau u. Konstruktion GmbH Elmshorn (MUK).
Benefit from the advantages of our cooperation!
Labelling robot - EMIL
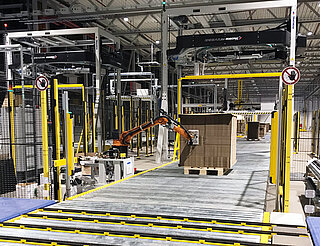
In order to relieve the machine operators, we offer you the possibility to apply pallet labels to your finished goods by means of a robot. This can be done after palletizing in front of or behind the strapping/wrapping machines. The blocks are tracked via the MINDA MoveIT and then the pallet labels are printed. The robot sucks in the pallet label, passes over a spray nozzle and sticks the packing label to the required customer position.
Palletizer - STRATOR
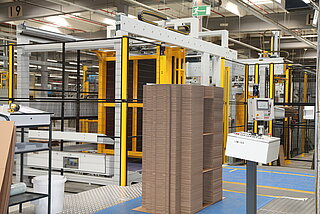
Apart from semi-automatic palletizing, MINDA now also provides fully automatic layer palletizing as an addition to its portfolio. The individual stacks or bundles are assembled to the desired layer pattern in the palletizer section. Thanks to the modular design, customer requirements can be implemented individually and accommodated in production in a space-saving manner. This means that the layers can be deposited alternately by the turning device and, if required, doubled or tripled. In addition, an automatic empty pallet infeed is possible. Of course, we only use our Spherical Cross and Spherical Table components to create the layer. By using them we do not use lifting movements and offer you a system that is as open as possible.
Palletizer - STRATOR Duo
To complete our peripheral portfolio, our Strator series offers automatic palletizing of your products. This ranges from palletizing a single stack using a Strator 1600 x 1600 mm up to forming two blocks next to each other in the Strator 2800 duo, optionally also as a single stacker up to 2800 x 1700 mm.
The provision of bottom sheets or empty pallets, dispensing of intermediate layers or their turning can be adjusted according to your individual needs. By means of our Spherical Cross / Table components, well known from the FRACTOR, the patterns are formed. Thus, we provide you with a system that is as open as possible, as there are neither shearing nor pinching zones. Even the smallest packages of 200 x 200 mm are transported safely over the flat transport surface.
Stacking corner with/without lifting table
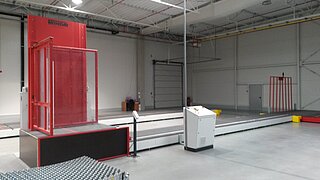
Stacking corners are used for manual stacking behind converting machines, when automatic palletizers are not used.
The stacking corner consists of a packing corner with adjustable side wall, which is in a pit or on an electrical lifting table.
In models with lifting table, the operator can raise and lower the lifting table by a foot switch. (ergonomic workplace)
Storage tower - CAPTOR
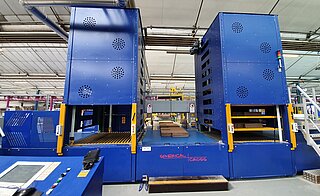
With the CAPTOR storage tower, you can control the destacking cycles behind your converting machines in order to process the output of the machines efficiently.
The buffering of packages in the storage tower in previously formed layers on the Spherical Cross enables an optimization of the personnel operating times. It is even possible to stack stacks from two die-cutters with only one palletizing robot by processing the output of the converting machines one after the other. The compact design and the storage on several levels provide the intermediate storage of several bundles. Even with very small space requirements.
In this way, as many stacks as possible are simultaneously collected in the storage tower and stored ready for delivery.
Unnecessary waiting times of the palletizer are avoided and the performance of the converting machines is increased.
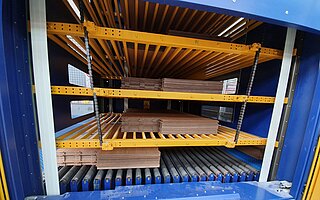
Once a layer has been completely formed, the next step is to lift the layer table under the roller conveyor and move it into the first buffer position. The layer tables are connected to each other at a defined distance, so that the second layer table is already positioned in the gaps of the roller conveyor when the first one is lifted out. This creates as small a gap as possible between the rollers, providing additional stability for the transported stacks. The layer is now buffered and a new empty layer is free for loading.
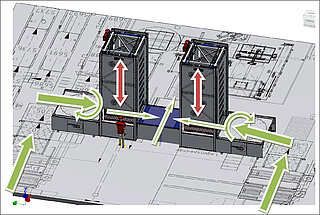
- Up to 9 layers per layer buffer
- Use of only one palletizer for two converting machines
- Intelligent storage and retrieval of bundles
Flyer Periphery behind converting machines
Further MINDA solutions for the corrugated board industry.
Our services and fields:
Our services and fields: