Finished goods transport
MINDA attaches great importance to a gentle transport adapted to the product when handling finished goods. Palletless goods are gently conveyed on plastic chains from the processing machine to the BOP loading station, to the high-bay warehouse or to the dispatch area. On the other hand, palletised goods are transported on frequency-controlled roller conveyors to prevent the goods from shifting when starting up. In hybrid systems, where both palletless and palletized goods are conveyed to the same extent, we constantly rely on transports on plastic chains.
Plastic chain conveyor for the finished goods transport
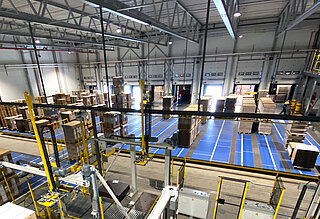
Plastic chain conveyors are used for the gentle transport of corrugated board stacks, whether as finished goods on pallets or without pallets.
Advantages:
• Flexibility in working width and length for each machine and adapted to local conditions
• Transport of all dimensions and even of heavy weights
• Dimensioning of the speed according to the machine capacities
• Smooth transport due to frequency-controlled drives
• As a standard, each conveyor is designed for a reverse operation
• Low maintenance
• High safety for the operators
• Suitable for palletless and palletised goods
• Complete visualization and material flow tracking on request
Turntable
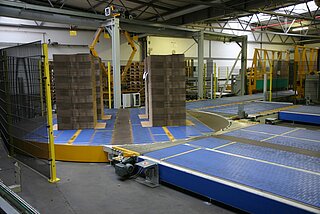
The standard task for a turntable is a change of the transport direction. With an appropriate size and the equipment with two parallel conveyors, up to four blocks can be picked up and turned simultaneously to meet the high performance requirements of transfer cars in the finished goods transport.
Advantages:
- Merging of several conveyor lines onto one central conveyor line
- Change of direction of the transport route without changing the orientation of the goods
- Variable dimensions according to the application
- Turntable with plastic chain conveyors for palletless goods
- Use of roller conveyors for goods being already palletized
- Combination of turntable and angular transfer system possible
- Angular corrections in conveyor lines possible
Right angle stations
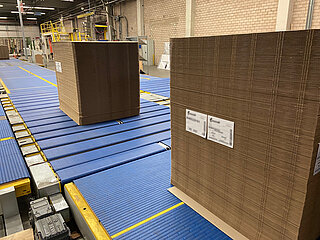
Right angle stations are used in the finished goods area where the transport direction changes by 90° and thus the length/width ratio. Furthermore, they can be used to bypass structural bottlenecks. To put back, store or buffer the goods, the realization of a loop with angular transfer systems represents a big advantage. Cycle peaks can be damped and downtimes prevented.
Advantages:
- Gentle surface transport of the goods, also of the lower sheets by using plastic chain segments in combination with plate link chains
- Suitable for palletized goods due to the robust and safe design by combining frequency-controlled drives of the conveying elements
- Variable number of segments according to customer requirements
- Large contact surface for the goods
- Suitable for all dimensions and qualities
- Compact and safe type of construction for use in different concepts
- Low maintenance operation
Transfer Car
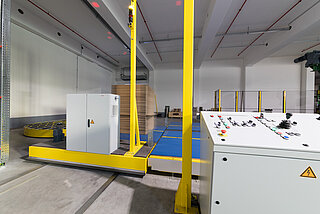
Transfer cars (shuttle cars) take over the task of cross shifting of blocks in the finished goods area.
Advantages:
- Keep work paths clear, therefore, good accessibility to the work areas
- Cycle-optimized realization of long distances
- Picking-up of multiple stacks
Control
Complex control of individual intralogistics systems
There is a complex control process behind the flexibility and the size of these intralogistics processes. This process also includes software solutions optimally adjusted to the individual conditions.
They are based on MINDA MoveIT, the control and visualization system for intralogistics programmed by MINDA.
The system coodinates the control of transport sections, floor conveyors and packing devices according to the plans of the ERP system.
This superordinated control based on PC is further internally developed by experienced programmers.
MINDA MoveIT guarantees a fully-automatic operation in all transport sections. The transport operations are optimized so that all storing places are efficiently used.
In the discharge area behind the corrugator the system exactly defines how and in which order and sequence the corrugated cardboard stacks reach the intermediate storage and the converting machines with an optimal utilization of the transport capacity.
These calculations are effected in real time and are the condition for continuous new evaluations of the prioritites of the individual operations.
Complete transport operation
The converting machines are supplied in time with goods for conversion according to the definitions of the ERP systems. After the conversion, the corrugated cardboard stacks are discharged from the machines and fed to the pallet protection. (picture 2) Here the correct pallet type is automatically prepared and the data for the strapping are available. The secured goods reach the finished goods storage and are ready for despatch.
The system flexibly reacts to inputs by the operators. During the entire production process the products can always be identified.
A dynamic visualization of the processes provides the customer an overview of the complete production flow.
Further MINDA solutions for the corrugated board industry.
Our services and fields:
Our services and fields: