Corrugator discharge
The discharge from the corrugator (corrugator) usually takes place over several sections. In the first section, the stacks are picked up by the corrugator. The second section rotates the corrugated boards optionally to change its orientation (cross-corrugated). Thus more stacks are transported and a space-saving transport to the connecting conveyors is achieved. The next section accumulates the stacks into blocks and can optionally perform a lateral stack doubling (cross opti) via a cross pusher. Thus the transfer car load behind the corrugator is fully utilized and a significantly higher performance is achieved.
Plastic chain conveyors for corrugator discharge
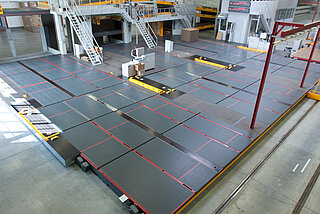
The full-surface plastic conveyors ensure the fast and gentle discharge of all stack qualities from the stacker of the corrugator.
Advantages:
- Large contact surface for the goods
- Fast discharge
- Transport of all qualities and formats processed
- Flexible working widths and lengths available for any application
- Transport without „sheet walk effect“
- Smooth transport through frequency-controlled drives
- Avoidance of damage to the bottom sheet of the stack, thus less waste
- Reduction of the risk of accident by a closed plastic surface
- Clean, easy-care surface
- Low maintenance expenses
- Complete visualization and material flow tracking possible
From the corrugator to the converting machines
Pop-up turning device
The 90° rotation of stacks behind the stacker of the corrugator provides several advantages:
- 90° rotation by a lifting cylinder at the zero line takes place in throughput, thus no loss of time
- Optimum storage utilization possible
- Sheet plant delivery can be aligned and optimized for the pallet
- Subsequent accumulation creates optimum load units for downstream means of transport or storage strategies
Doubling pusher
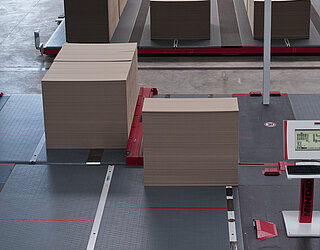
The cross pusher behind the stacker of the corrugator offers several advantages:
- Sheet plant delivery can be assembled and optimized for the pallet
- Creates optimum load units for downstream means of transport or storage strategies
- In combination with our accumulation system, modern and new corrugators are optimally evacuated
Palletizing pusher
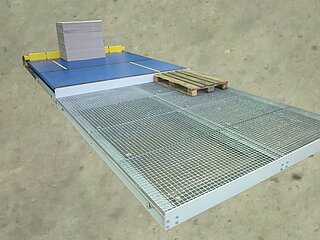
If the corrugator and further converting machines are not connected to the conveyor technology, palletizing pushers are used behind the discharge line of the corrugator in order to position the stacks of sheet goods on pallets.
If it is not possible to load empty pallets and discharge the palletized goods laterally, for example due to space constraints, empty pallets can be fed and the palletized goods transferred in a minimum of space using a palletizing pusher.
Turntables
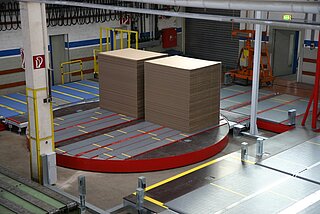
Turntables with two parallel plastic chain conveyors are used in the corrugator discharge when the transport direction has to be changed by 90°. Two blocks of small chop length can be rotated next to each other or one large block can be rotated by coupling both conveyors.

If a space-saving change from lengthwise to crosswise transport is required in straight direction, the turntable can be equipped with a right angle station.
Pallet loading station BOP

Pallet loading station for single stacks
The pallet loading station as single loading station is used to load a block for sheets as well as for finished goods. Block lengths and widths from 500 mm to 1,800 mm or from 500 mm to 2,100 mm can be palletized with a minimum stacking height of 400 mm. A maximum of 120 to 140 loads can be put on pallets per hour.
Thanks to its extremely compact design, a single loading station can be easily integrated into existing systems.
Single or double loading station
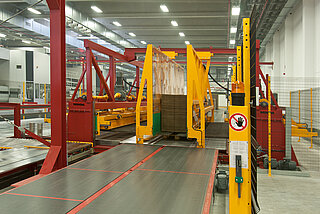
Single resp. double loading stations are used for the transport of sheets, when a large-size block of, for example, 2.4 x 5.0 m is to be positioned on pallets. Up to 100 blocks can be palletized per hour. It is, however, also possible to palletize two blocks of smaller sizes, e.g. 2.4 x 2.4 m or 1.6 x 1.8 m, of the same width in one cycle. Up to 200 blocks are palletized per hour. These models can be used for sheets as well as for finished goods.
Pallet loading station with divided walls
The walls and the pusher are separated and separately driven to allow loading of different block widths in one work cycle. For longer blocks, the walls and the pusher are displaced at the same time and only one block is placed on the pallet.
Empty pallet robot P-DROID
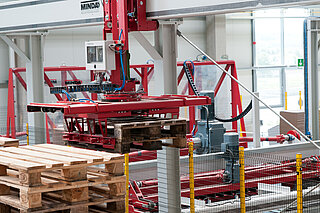
The empty pallet robot takes the empty pallets from the pallet stack and deposits them one after the other in the desired direction during pallet preparation. The pallets are pushed off by 90°. Depending on the requirements, a defined pallet pattern is created.
The pallet pusher laterally pushes the pallets under the pallet loading station, where the pallets can be positioned according to definition. The pallets can be taken or deposited in lengthwise and crosswise direction at high speed. Several types of empty pallets can be used in parallel.
In order to increase the performance, it is possible to take two pallets from the stack at the same time and to deposit them individually.
Pallet loading center installed in Austria
In a pallet loading station sheets as well as finished goods can be positioned on pallets. The protection sheet dispenser fully-automatically applies a bottom edge protection which is required for the strapping process. The empty pallet robot positions the empty pallets. Upon demand it is also possible to create pallet patterns in the feeding section. A capping material robot applies top pallets, panels and grids.
Finally the palletized material is automatically strapped and stretched.
Control
Complex control of individual intralogistics systems
There is a complex control process behind the flexibility and the size of these intralogistics processes. This process also includes software solutions optimally adjusted to the individual conditions.
They are based on MINDA MoveIT, the control and visualization system for intralogistics programmed by MINDA.
The system coodinates the control of transport sections, floor conveyors and packing devices according to the plans of the ERP system.
This superordinated control based on PC is further internally developed by experienced programmers.
MINDA MoveIT guarantees a fully-automatic operation in all transport sections. The transport operations are optimized so that all storing places are efficiently used.
In the discharge area behind the corrugator the system exactly defines how and in which order and sequence the corrugated cardboard stacks reach the intermediate storage and the converting machines with an optimal utilization of the transport capacity.
These calculations are effected in real time and are the condition for continuous new evaluations of the prioritites of the individual operations.
Complete transport operation
The converting machines are supplied in time with goods for conversion according to the definitions of the ERP systems. After the conversion, the corrugated cardboard stacks are discharged from the machines and fed to the pallet protection. (picture 2) Here the correct pallet type is automatically prepared and the data for the strapping are available. The secured goods reach the finished goods storage and are ready for despatch.
The system flexibly reacts to inputs by the operators. During the entire production process the products can always be identified.
A dynamic visualization of the processes provides the customer an overview of the complete production flow.
Further MINDA solutions for the corrugated board industry.
Our services and fields:
Our services and fields: