Intermediate storage on one or two levels, up to the solution of a high-bay warehouse
MINDA offers various concepts for an intermediate storage. Intermediate storage as area storage with conveyor widths, individually adapted to your needs, is the classic variant of intermediate storage. The intermediate storage is divided into several sections in order to sort the orders order-related and format related and feed them to the processing machines. Even a product mixture in the intermediate storage does not represent a problem thanks to the higher-level MINDA control system. You will never have a BlackBox again and keep complete control over your intermediate storage.
Due to the increasingly precious need for space, MINDA also offers you a two-level intermediate storage system. Furthermore, the product portfolio includes in-house storage systems, cube systems and high-bay warehouses.
There are two different concepts for two-level intermediate storages. One has got a central transfer car which can distribute the stacks into the lower and upper level via a lift. However, this concept must be locked off from the outside. The storage area is, therefore, not accessible, as the falling down of stacks represents a safety risk. The second concept has got transfer cars on both levels and the stacks are conveyed to the second level via a lifting station. We take your special conditions on site into consideration and are happy to work out a suitable solution together with you.
Plastic chain conveyor in the buffer store

The full-surface plastic conveyors offer several advantages in the intermediate storage:
- Optimum warehouse utilization by coupling several conveyors
- Flexible working widths and lengths available for any application
- Gentle transport and avoidance of damage
- Transport of all qualities and formats processed
- Transport without „sheet walk effect“
- Smooth transport by frequency-controlled drives
- Reverse operation mode
- Clean surface easy to clean
- Low maintenance expenses
- High safety for the operating personnel
- Complete visualization and material flow tracking
Vertical lift

Vertical lifts connect two or more levels in order to return tools, printing plates and colors back into the warehouse. They can also be used for heavy piece goods.
Advantages:
- Low maintenance compared to cable elevators
- Execution with or without conveyor technology
- High lifting and lowering speeds
- No pit required
- Increased safety by two lifting belts each
- Lean, space-saving construction
Double- or three-level intermediate storage
Application:
- when there is not enough space on one floor
- can also be designed in three levels
- safe discharge from one or serveral corrugators for all sizes and speeds
- continuous supply of all machines for further processing and a direct line for articles for sale
- gentle fully-automatic stack transport
- reduction of waste material
- increased production by intelligent material flow control
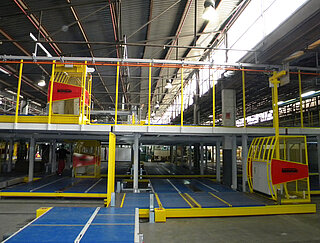
Advantages:
- space-saving, optimal utilization of space especially regarding the height of the hall
- high throughput
- possibility of resorting from stage to stage or from floor to floor
- electrical lifting devices on transfer car
- camera monitoring of top floor
- simple and efficient protection of double- or three-level storage
- utilization of other floors to store printing plates, colours and tools
Transfer car
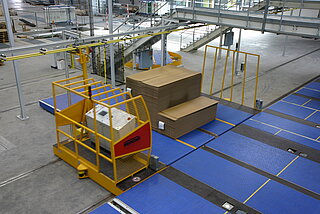
Automatic stack transport from intermediate storage to converting machines
Different executions for stack transport in the intermediate storage and to the converting machines are available.
Advantages of all models:
- speed up to 150 m/min
- several conveyors to accepts goods of different orders possible
- vulcollan wheels/ servo-drive for vibration-free operation
- sinusoidal acceleration and deceleration curves to ensure smooth start-up and stopping for optimal transport
Different executions for stack transport in the intermediate storage and to the converting machines are available.
Transfer cars with two decks
The fully-automatic transfer car is available with two decks to transport four different loads in one transport cycle.
Transfer car with four decks
Moreover, the transfer car can be provided with four decks to transport eight different loads in one transport cycle. This capacity makes it possible to handle the increasing transport volumes of modern machine lines.
Transfer car with lifting device
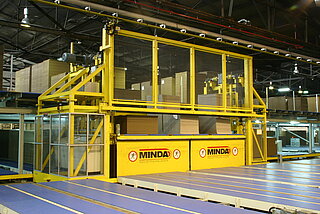
The transfer car is equipped with a lifting device to feed the second floor of an intermediate storage.
Lifting is electrically by means of expansion resistant flyer chains and it is effected during the operation of the transfer car. This transfer car corresponds to the German safety standard BGI 854.
Control
Complex control of individual intralogistics systems
There is a complex control process behind the flexibility and the size of these intralogistics processes. This process also includes software solutions optimally adjusted to the individual conditions.
They are based on MINDA MoveIT, the control and visualization system for intralogistics programmed by MINDA.
The system coodinates the control of transport sections, floor conveyors and packing devices according to the plans of the ERP system.
This superordinated control based on PC is further internally developed by experienced programmers.
MINDA MoveIT guarantees a fully-automatic operation in all transport sections. The transport operations are optimized so that all storing places are efficiently used.
In the discharge area behind the corrugator the system exactly defines how and in which order and sequence the corrugated cardboard stacks reach the intermediate storage and the converting machines with an optimal utilization of the transport capacity.
These calculations are effected in real time and are the condition for continuous new evaluations of the prioritites of the individual operations.
Complete transport operation
The converting machines are supplied in time with goods for conversion according to the definitions of the ERP systems. After the conversion, the corrugated cardboard stacks are discharged from the machines and fed to the pallet protection. (picture 2) Here the correct pallet type is automatically prepared and the data for the strapping are available. The secured goods reach the finished goods storage and are ready for despatch.
The system flexibly reacts to inputs by the operators. During the entire production process the products can always be identified.
A dynamic visualization of the processes provides the customer an overview of the complete production flow.
Further MINDA solutions for the corrugated board industry.
Our services and fields:
Our services and fields: