Requirements for the control technology of a system
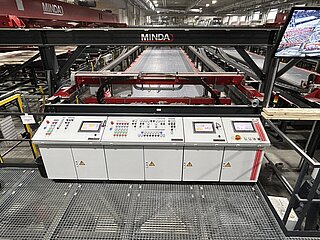
In addition to solid and efficient mechanics, control technology is becoming increasingly important:
- Flexible systems with extensive functions for a wide production range
- High degree of automation - low in personnel
- High operating comfort
- Complex interfaces within the system and possibly to upstream production planning.
Control technology from MINDA
To guarantee the optimum solution in the field of electrical and control technology, we take the hardware planning, the drawing of the wiring diagrams, the PLC programming and the commissioning into our own hands. Due to the close cooperation between our mechanical design department and the electrical engineers and programmers, the mechanical, electrical and control systems are perfectly matched.
Our systems are designed for fully automatic operation. Nevertheless, situations may arise in which the operators have to intervene in production on site. For this purpose, we work closely with you to place the operator terminals at key points. These ones are equipped with touch panels on which machine status and error messages are displayed. The operator can also enter or change production data if required. For manual operation of the system, we use user-friendly buttons and rotary switches that have well proven for the solid wood and sawmill industry.
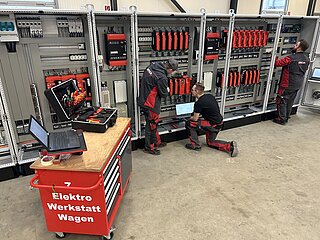
Our control cabinets are exclusively equipped with high-quality components from well-known manufacturers. This ensures a maximum availability and a long supply with spare parts. We also pay attention to energy efficiency. For this purpose, we use the latest generation of drives and converters and feed braking energy back into the network wherever possible.
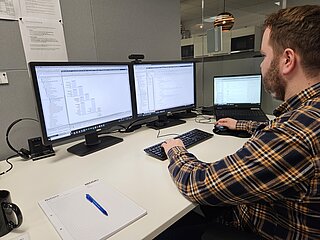
Use of software proven millions of times
With the fail-safe SIMATIC S7-1500 controllers, we rely on maximum performance and built-in future security. The modular control system enables us to implement sophisticated machine concepts, including the required safety functions, and reliably accompanies you on your path to digital transformation.
The fail-safe connection of the input/output signals of the safety function is carried out via corresponding signal modules (centralized/decentralized) or via PROFIsafe-capable devices.
To ensure that your systems are state-of-the-art, we always use the latest versions of the Siemens TIA portal for the program creation. We use the programming languages offered by Siemens. We mainly use AWL, but also increasingly SCL, to be able to utilize the full performance spectrum of the controllers.
Both our program structures and our hardware are designed in such a way that data can be easily exchanged with the higher-level Manufacturing Execution System (MES) via the plant's internal Ethernet.
Communication within our systems and with external devices is made via PROFINET. This is the leading industrial Ethernet standard for automation at field level.