Cross Laminated Timber (CLT) plants
Already in 2010, after an intensive development phase, we launched our first cross laminated timber line with a TimberPress X 300 for an industrial cross laminated timber production. In the meantime, more than 20 cross laminated timber lines in various executions have proven themselves on the market worldwide.
With the use of our modules for material handling and conveyor technology as well as our control technology, we adapt to existing buildings and lines but we also realise Greenfield projects.
We optimize our line planning to the desired production volume. In our projects being realised so far, one, two or three cross laminated timber presses with a total output of up to 50 boards/hour have been used.
Most of our implemented projects are designed for a flexible production - batch size 1 - with corresponding requirements for the degree of automation and the control technology.
For us, batch size 1 means 100 % flexibility both in terms of the CLT panel dimensions and the panel structure. Wall and ceiling elements with completely different panel dimensions can be produced in any order.
In addition to flexible lines for batch size 1, we have also planned and commissioned lines for series production of standard elements, too.
Apart from the increase of performance, a particular focus of development in recent years has been the improvement of resource efficiency to ensure a wood-saving production as best as possible. With our TimberPress X 100 eco, we delivered the first CLT press in 2020 producing fully automatically cross laminated timber panels with window and door cut-outs.
CLT production in Estonia
For this project, MINDA developed a concept for a flexible CLT production that would ensure a strong production performance and a high degree of automation. Special designs should still be possible.
On a manageable area of 2100 m², a modern CLT production facility was built with an annual production of up to 40,000 m³ of CLT with two-shift workload.
The CLT elements are pressed from "loose lamellas" using PUR glue.
This process takes place in the hydraulic press TimberPress X 336, length and cross compression included. Thus, panels are created consisting of three to ten layers with a width of 2,050 to 3,600 mm, a length of 3,000 to 15,200 mm and a thickness of 40 to 350 mm.
After pressing, the CLT blanks are sanded.
Depending on the quality requirements, the CLT elements can be assessed from both sides via an element turning device and, if necessary, can be repaired. The entire line is designed for batch size 1 and is controlled by the higher-level MINDA production control system. This one is linked to customer's work preparation system.

and PUR-glue application system
and element turning device
and PUR-glue application system
and element turning device
Location: Estonia
Space requirement: 2100 m²
Starting material: unplaned panels
Finished product: large-size CLT panels
Length: 3,000 – 15,200 mm
Width: 2,050 - 3,600 mm
Thickness: 60 - 350 mm
Press type: TimberPress X 336
Glue: 1K - PUR
Number of operators: 2
Batch size: 1 - production to order
Legend:
1. Feeding of finger jointed and planed lamellas
2. Cross-cut saw: Cutting of the respective lamella length
3. Buffering of length layers
4. Buffering of cross layers
5. Vacuum laying portal and PUR-glue application system: Formation of the glued CLT element
6. Laying area: Simultaneous change of press charge
7. TimberPress X 336: Hydraulic CLT press with integrated, three-dimensional compression of the glued CLT element
8. Onward transport of CLT elements: To quality control and sanding machine
9. Quality station and element turning device
10. Surface sanding machine
11. Picking-up station of sanded CLT elements going to the CNC-joinery lines
Overview of the CLT production
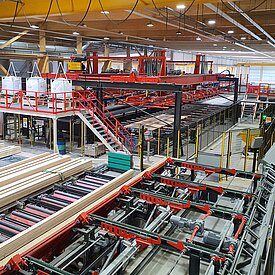
Lamella curing storage and line feeding
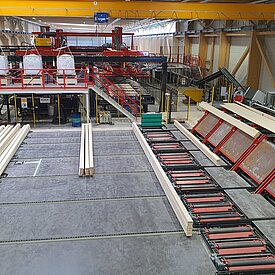
Vacuum laying portal
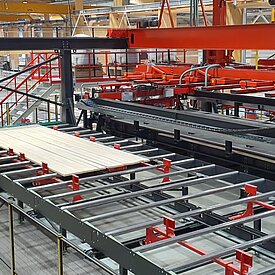
TimberPress X 336
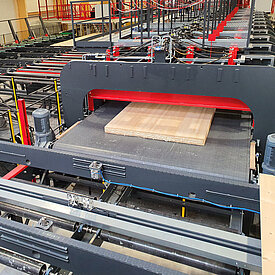
CLT production in Sweden
An existing post and beam production line should be converted into an efficient and flexible CLT production line at lowest cost possible. The existing production hall was too small for a standard CLT layout and at first glance did not offer sufficient space for the production of large-sized cross laminated timber boards.
Together with the customer's project team, we developed a solution proposal that fully takes into account all boundary conditions. The result is a very compact and yet functional cross laminated timber production line on an area of 90 m x 20 m, being supervised by only 2 employees.
A maximum of 16.6 m x 3.1 m CLT elements can be pressed on the line at a maximum pressure of 0.8 N/mm² / 117 psi.
The line is operated in two shifts with an annual production output of approx. 30,000 m³ of cross laminated timber. The production is flexibly designed so that in batch size 1 the elements required on the construction site are pressed and processed exactly in the right order. The changeover to the respective CLT element is done quickly and flexibly.
The FlowMate master computer system installed by MINDA ensures a smooth production workflow. It stands for high process reliability, user-friendliness and also provides data for customer's quality management.
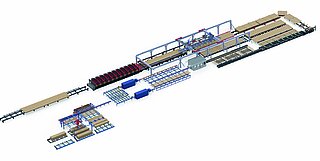
and PUR glue application
and PUR glue application
Location: Sweden
Space requirement: 110 x 20 m
Starting material: unplaned panels
Finished product: large-size CLT panels
Length: 8,000 x 16,600 mm
Width: 2,050 x 3,100 mm
Thickness: 60 - 350 mm
Press type: TimberPress X 331
Glue: 1K - PUR
Number of operators: 2
Batch size: 1 - production to order
Legend:
1. Vacuum destacker: Automatic line feeding with different dimensions and qualities
2. Control area and quality assessment: Production sequence control with monitoring function
3. Finger-jointing lines: Two compact finger jointing lines for lamella production
4. Lamella planer: Four-sided planer
5. Transfer buffer incl. lamella turner: Intermediate storage of length and cross layer lamellas
6. Buffer for length layers: Buffering of a maximum of 4 length layers
7. Crosscut saw: Cut to length of cross lamellas
8. Buffer for cross layers: Buffering of a maximum of 4 cross layers
9. Vacuum laying portal and PUR glue application: Formation of the glued CLT element
10. Laying area: Simultaneous change of the press batch
11. TimberPress X 331: Hydraulic CLT press with integrated, three-dimensional compression of the glued CLT element
12. Transport of the CLT elements to the joinery lines and commissioning/shipping
Formation of length layers
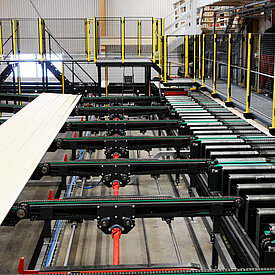
Feeding of length and cross layers
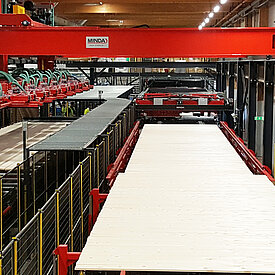
Support of length lamellas
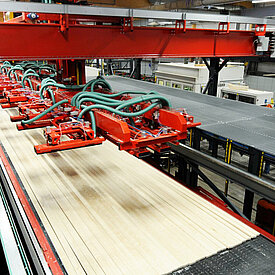
Glue application

Press blank before compression
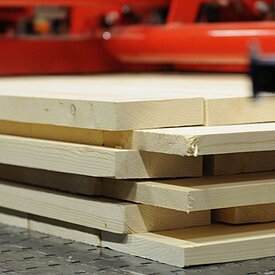
Pressing of a five-layer CLT element
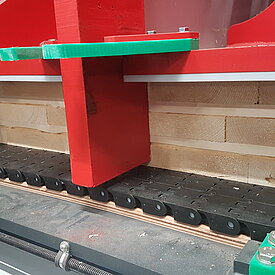
TimberPress X 331
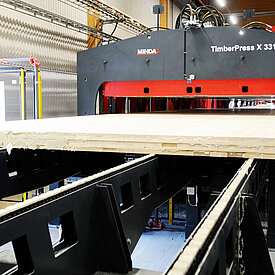
Pressed CLT element
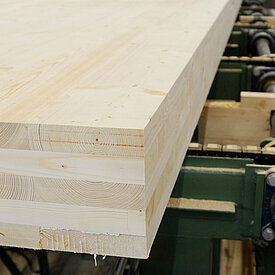
CLT production in the U.S. (rig mats)
This production line for manufacturing small-sized CLT panels was designed for a very high production output. A special performance demand was made on feeding the three CLT presses which are working side by side.
The hydraulic presses were designed to enable a cycle time of 20 minutes. With a single-shift workload, an annual capacity of up to 250,000 elements is achieved. The press chambers with a height of 1.20 m allow, for example, the pressing of 8 x 3-layers or 5 x 5-layers panels in one pressing process. The pressing pressure is designed for up to 0.65 N/mm² / 95 psi, whereby the pressure is supplied in vertical direction.
The three- to five-layers CLT panels which are produced on this line are manufactured in standard sizes and are used as temporary roadways. Two lamella are eliminated from each lower layer for better adhesion to the ground. They are used as so-called "access mats" or also "rig mats", for example, in the oil sand industry or during the erection of wind turbines in impassable terrain.
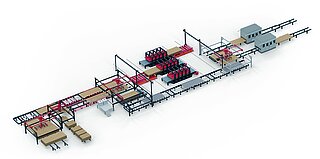
including glue application
via a shuttle
including glue application
via a shuttle
Location: USA
Space requirement: 125 x 40 m
Starting material: planed panels
Finished product: Roadway slabs
Length: 4,260 – 5,490 mm
Width: 2.440 mm
Thickness: 114 - 165 mm
Press type: TimberPress X 225
Glue: 1K - PUR
Number of operators: 4
Batch size: Series production
Legend:
1. Feeding of length layers: Vacuum destacking and separation
2. Feeding of cross layers: Vacuum destacking and separation
3. Formation of the press package including glue application
4. Feeding of the CLT presses via a shuttle
5. TimberPress X 225: three hydraulic presses standing next to each other
6. Formatting: Cutting to the final size
CLT production line
For a Scandinavian customer, MINDA designed a flexible plant concept for the production of large-sized CLT elements.
Panels of maximum 16.60 m x 3.10 m can be pressed on a hydraulic CLT press, the TimberPress X 331.
The MINDA MCS computer system ensures a smooth production workflow.