Individual solution for car body construction
The car body forms the outer shell of rail vehicles - with a great influence on safety and comfort as well as on costs and performance.
Today car bodies are mostly modular design. They consist of individual modules/ segments, which are often produced in small series. Product-specific devices are used for the production of individual segments.
Based on our many years of experience, we develop and manufacture clamping devices, special welding devices and various other application-specific devices for car body construction. In addition to pneumatic and hydraulic clamping technology, electromagnetic clamping technology is also used.
Product examples of tailor-made devices for car body construction
Magnetic clamping device for car body laser welding machines
This customer-specific clamping device is used for laser welding of complete body components for rail vehicles nd it represents a negative of the outer vehicle contour. After the device has ben equipped, this rail-bound device drives into the laser welding cabin on rails.
Structure of the device
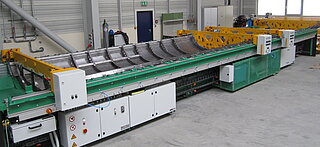
The device consists of a movable base frame with independent drive. The component support is equipped with magnets, which can be switched on in different groups.
In the extentionof the clamping device there is a so-called clamping bridge station. This contains various clamping bridges for positioning, clamping nd holdingduring tacking and welding. Furthr assembly parts, which can be fastened to the component support, complete the device.
Functions of the welding device
All contour-rolled sheets, reinforcements and framework structures are electro-magnetically clamped, controlled by programs. Mounting parts are positioned by the clamping bridges.
First, the roof cladding sheets are welded together. Indicator lights show the operator the position and number of clamping bridges required for tacking the cross beams. Then further parts are positioned, clamped, tacked and welded by means of clampingbridges and other device elements.
Efficiency through electro-permanents magnets
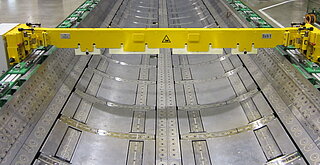
Clamping and unclamping with electro-permanent magnetic clamping plates is done by magnetizing or demagnetizing through a current surge.
By subdividing the entire clamping surface into individual magnetic groups, different assembly groups can be welded on the same device. Adjusted to the workpiece contours, regulary distributed high clamping and holding forces are generated.
A considerable reduction in set-up times leads to shorter downtimes and thus to an increase in productivity. Reduced maintenance costs by less wear complete the advantages and the resulting benefits of this magnetic clamping device.
Technical data
All data can be adjusted to customer- or application-specific requirements.
Dimensions of the device: | Total height: | approx. 1,250 mm |
Total width: | approx. 3,000 mm | |
Total length: | approx. 15,350 mm | |
Weight: | approx. 22,000 kg | |
Number of traction drives: | 2 | |
Number of clamping bridges: | 9 |
Benefits/ advantages
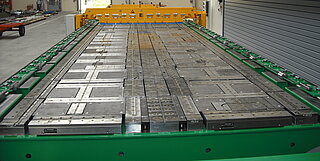
- automatic positioning and clamping processes
- clean joining of profiles (welding gap "0")
- short changeover and set-up times
- high repeat accuracy
- high process reliability
- can be used for different variants
Universal welding device for side walls
This customized welding device is used for aligning, joining, fixing and positioning flat or curved profiles for welding side walls of long-distance trains.
Structure of the clamping and welding device
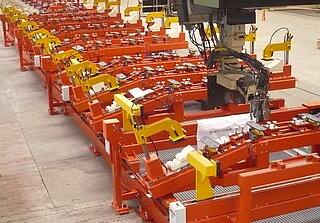
The approx. 24 m long base frame is characterized by a solid and divided modular design. It consists of several segments which are screwed together.
Along the longitudinal carriers there are adjustable suspension devices for mounting, lengthwise displacement and locking of the cross carriers. The device includes 10 crossbars and 7 joining units.
Further components of the welding device are 4 turning devices, which are required for turning the assembly group. Limit stops and various accessories complete the device.
Between the longitudinal carriers of the base frame, the base frame is equipped with gratings so that an increased working platform is created for retooling.
Functions of the clamping and welding device
For each sidewall type to be manufactured, there are defined positions for the joining units and crossbars. These are set at the beginning. For this purpose, labels are attached to the base frame where the respective position for the sidewall type can be read. Markings facilitate the alignment.
The individual profiles are inserted, aligned and clamped into the corresponding joining units and crossbars. Then the front side is welded by the robot system.
After welding the front side, the assembly group is turned by means of the turning device. Finally, the back side can also be welded.
Technical Data
All data can be adjusted according to customer`s or application-specific requirements
Dimensions: | Length: | 26,170 mm |
Width: | 4,980 mm | |
Hight: | 2,350 mm | |
Supporting hight: | 1,362 mm | |
Traction forces: | 40 Vacuum suction cups | |
60 Clamping cylinders | ||
20 Hydraulic cylinders | ||
Compressive forces: | Clamping cylinders | |
Hdraulic cylinders |
Benefits/ Advantages
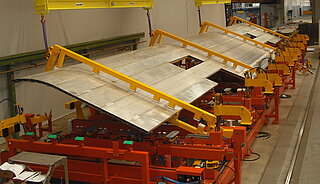
- applicable for different types of wagons
- positioning, joining and clamping proceses are program-controlled
- clean, precise joining of profiles ("welding gap "0")
- short changeover and set-up times
- high repeat accuracy
- high process reliability
- high maintenance friendliness
- easy cleaning
Welding device for side walls
In this customer-specific welding device, two side walls of approx. 20 m each can be positioned on behind the other. The side walls welded together from aluminium profiles are completed with prefabricated door parts or assembly groups.
All supporting frames can be moved and locked in y-direction over the entire length of the device. Thus, a new configuration of the device is possible so that other sidewall types can also be processed at short notice.
The positioning is done in the straight contour area. The supports provide the required flatness without complex readjustment procedures. After positioning the side walls, the clamping elements are positioned and fixed out of the hanging position above the side wall.
Assembly groups of the special device
- base frame with lateral rail and working platform made of grids
- 8 individual stands with 2 horizontal spindles each for pre-tensioning
- 4 double stands with intermediate platform
Technical data
All data can be adjusted according to customer`s or application-specific requirements
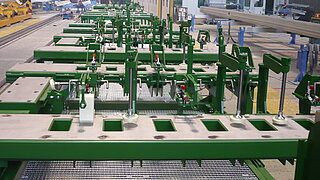
Dimensions:
Length: 40.000 mm
Width: 2.330 mm
Hight: 1.030 mm
Benefits/ advantages
- applicable for different types of side walls
- short changeover and set-up times
- high repeat accuracy
- high process reliability
Further MINDA solutions for railway technology devision
Our services and fields: